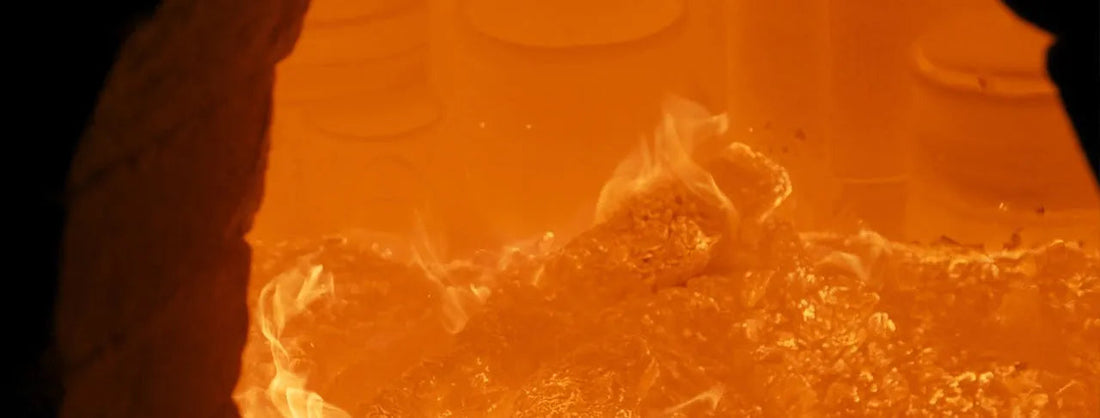
Ceramic firing: A guide to perfect processing
Share
Firing Ceramics: A Guide
Reading time: 10 minutes
[Update: April 18, 2025]
Firing is one of the most crucial steps in ceramic production. It not only adds strength and durability to the piece, but also significantly determines the appearance and texture of the finished product. Firing techniques and temperatures vary depending on the type of ceramic and the desired results. In this comprehensive guide, you'll learn everything you need to know about the firing process and how to optimize it for perfect ceramic pieces.
The two main firing methods: bisque firing and glaze firing
bisque firing
The bisque firing is the first firing process a ceramic piece undergoes. It takes place at a temperature of approximately 600 to 950 °C and serves to harden the piece, giving it a stable shape. The bisque firing also removes excess moisture from the clay, making the ceramic body stable while still remaining porous. This porosity is important for the proper absorption of the glaze in the next step.
A crucial aspect of biscuit firing is temperature control. If the temperature is too high, the clay can crack if it cools too quickly. Biscuit firing should be carried out in a slow, controlled process to achieve optimal results.
Glaze firing
Glaze firing is the second firing process, during which the glaze is applied to the piece and melted at temperatures between 950 and 1400 °C. This high temperature ensures that the glaze takes on its final shape and texture, forming a durable surface. Glaze firing not only gives the ceramic its color and glossy surface, but also makes it waterproof and more resistant to wear.
A successful glaze firing depends on the correct selection and application of the glaze. Depending on the glaze and firing technique, various surface textures such as matte, glossy, or even mottled can be achieved. Glaze firing is also the process in which the desired color intensity and final finish of the piece are determined.
Important factors when firing
Firing temperatures
Firing temperatures vary depending on the type of clay and glaze. Different clays require different firing temperatures to achieve the desired physical properties and appearance:
- Earthenware : 1000 to 1200 °C
- Stoneware : 1200 to 1400 °C
- Porcelain : 1200 to 1400 °C
- Clay : 600 to 950 °C (biscuit firing)
The exact temperature should always be monitored and adjusted, as temperatures that are too high can deform or damage the piece, while temperatures that are too low can result in the glaze not melting properly or the ceramic piece not being sufficiently durable.
The right kiln
Various kilns are used for firing ceramics. The most commonly used kilns are:
- Electric kilns : These kilns are particularly suitable for glaze firing because they allow precise temperature control and are often used in oxidation firing processes.
- Gas kilns : Gas kilns are the preferred choice for reduced firing, which lowers the oxygen level in the kiln to achieve unique, rustic color and surface textures.
- Wood-fired kilns : Traditional pottery workshops sometimes use a wood-fired kiln to achieve a distinctive, irregular surface texture. However, this firing process requires more experience and is more difficult to control.
An important consideration when choosing a kiln is the size of the kiln relative to the number of ceramic pieces to be fired. Overcrowded kilns can result in uneven temperature distribution, resulting in uneven firing results.
Additional firing techniques: reducing and oxidizing firing
When firing ceramics, various firing techniques are often used, each of which affects the colors and textures of the ceramic. Two particularly interesting techniques are reduced firing and oxidation firing.
Reducing burning
During reduction firing, oxygen is removed from the kiln, resulting in a chemical reaction that influences the colors of the glazes and clay. This process creates a distinctive, rustic look, particularly emphasizing earth tones and warm tones. Reduction firing is often performed using gas kilns, as these allow for controlled oxygen levels.
Reduced firing is particularly popular in Raku pottery, where the piece is removed from the kiln after firing and quickly placed in cold materials such as sawdust or newspaper to achieve dramatic color changes.
Oxidizing firing
In contrast, oxidative firing ensures that the kiln is filled with excess oxygen. This method results in a clearer and more vibrant glaze color, which is particularly used in electric kilns. The colors are often brighter and the surface texture smoother. Oxidative firing is the preferred technique for uniform glazes and precise coloring.
Both firing techniques offer unique aesthetic results and are relevant for various creative goals and applications.
Tips for successful distilling
Here are some valuable tips that can help you optimize your firing processes and achieve the best results:
- Temperature monitoring: Invest in a high-quality thermometer and a reliable thermocouple to accurately monitor oven temperatures. Small temperature fluctuations can have a big impact on the final result.
- Slow cooling: Allow the kiln to cool slowly, especially after the glaze firing. Cooling too quickly can lead to cracks and breakages in the piece.
- Using firing agents: If you want to achieve a specific color or texture, experiment with firing agents such as ash, salt, or tin. These can create exciting effects on the surface of your ceramic.
- Test firings: Conduct test firings before firing large pieces or collections of pottery at once. This will help you determine the best firing parameters for the specific clay and glaze.
- Raku technique: When working with the Raku technique, be sure to quickly transport the pieces to the cool area after firing and place them in containers filled with sawdust to stop the oxidizing process.
Opinion of pottery
At Töpferkunst, we place great importance on the quality of our ceramic products. We prefer to work with the utmost precision, tailoring both bisque and glaze firing to the exact characteristics of the respective clay and design. This ensures that our tableware is both functional and aesthetically pleasing. Our ceramics are carefully fired to provide you with products that impress with both design and durability.
Conclusion
Firing ceramics is a fascinating and crucial process that gives pieces their final form and function. Proper handling of firing temperatures, kilns, and firing techniques is crucial to ensuring the quality and durability of the ceramics. Whether bisque firing, glaze firing, or special techniques such as reduction and oxidation firing – every step requires precision and experience. Those who delve deeper into the subject of ceramic firing will discover a world of creative possibilities and endless variations waiting to be explored.
If you would like to learn more about the art of ceramic firing, you will find helpful resources on the firing process and ceramic production at Keramiko.de .
Check out our Color collection to get a feel for the result of perfectly fired ceramics!